With the rise of more and more fresh food and cold fresh e-commerce, cold chain logistics and cold chain storage have become the core issues that limit the growth of enterprises. In order to optimize the application of cold storage, the group plan and planning of shelf system in cold storage played a vital role. Here’s XINMIAO to take you to understand some standard knowledge of cold storage racks:
The design of cold storage racks is similar to that of ordinary warehouse racks. There are no special requirements for the design and production of ordinary warehouses, but the cold storage has certain requirements for materials and anti-rust coatings, which is also in the design is different from ordinary warehouse racks.
The storage racking systems of cold storage generally use high level racks, and even automation is implemented on this basis, and the cost of cold storage is very high.
The normal temperature is below minus 16 degrees, so the thermal insulation performance of the warehouse and the rationality of the rack design are very important. The former can reduce the cost of electricity, and the latter can reduce the cost in terms of increasing the storage space and improving the efficiency of access and inventory.

Drive-in racks: This type of rack has low investment cost and high storage density. It is suitable for storing large quantities and few types of goods. The access mode of goods is the first deposit and then withdrawal. Forklift storage efficiency is high and reliability is strong. It is suitable for most Handling machine storage jobs.
Radio shuttle racks: This type of rack is the same as the drive-in rack and can be used with shuttle car. The cost is medium and low. The rack channel and the storage device are equipped with the operation channel of the deployment (traveling vehicle), and the forklift is only on the rack. The two heads load and unload the goods to the racks, and the pallet goods are transported from the inbound end to the outbound end by the crossing vehicle.
Push back racks: The technology of push back racks has a high space utilization rate and is easy to access. The total depth of the racks is within 6 pallet depths, the unit weight of goods is within 1500kg, and the rack height is under 6m. The principle of failure after generation, the forklift does not need to enter the storage channel, and is operated at the lower end, and the push back rack is suitable for cold storage and places with low requirements for product sorting.
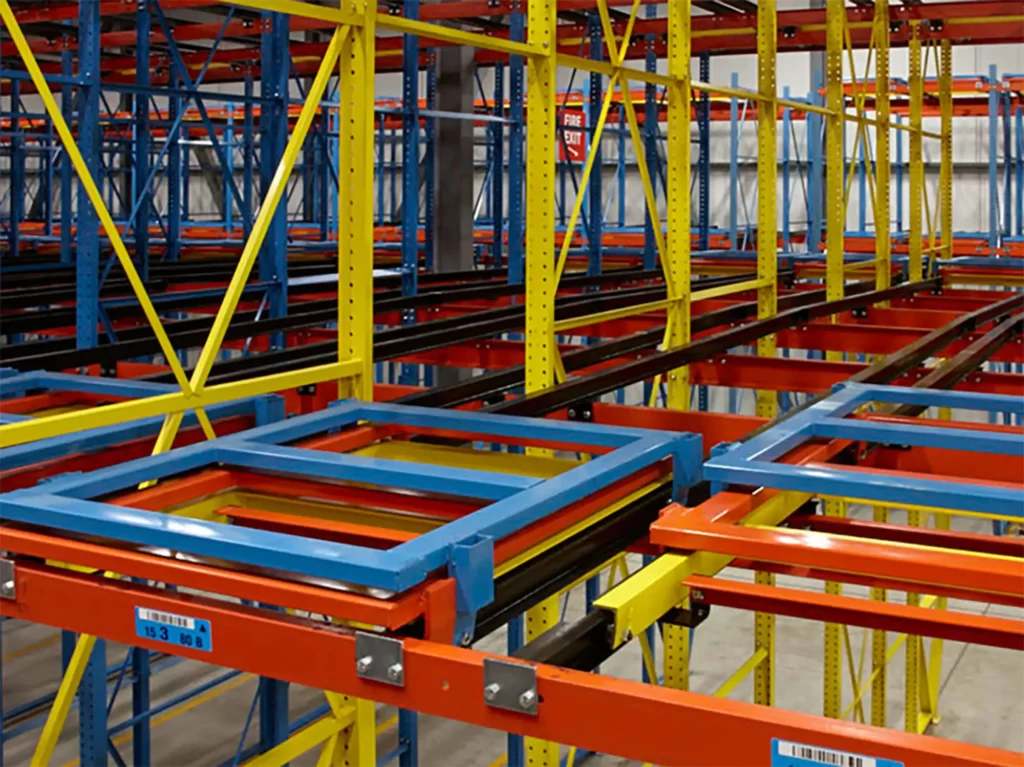
Beam rack: Beam rack is easy to access, easy to install and disassemble, easy to install and disassemble, low cost, elegant appearance, fair design, strong bearing capacity, unit high load capacity up to 5t, humanized solution, floor height can be adjusted freely, Plug-in combined type, no need for welding and screwing, easy to transport.
Narrow aisle (VNA) racks: adopt narrow-aisle forklifts to store and take pallets from the narrow-aisle racks on the two sides of the aisle. The fork of the narrow aisle (VNA) forklift has three-way rotation and side shifting, so the forklift does not need to turn at a right angle when picking up and storing pallets in the aisle, and the narrow aisle rack can be used in various industries.
Factors to consider when designing cold storage racks:
When designing cold storage racks, you first need to identify the cold storage.
For high-temperature cold storage, the product temperature needs to be controlled between 0 °C and 4 °C or 6 °C. Products with many storage types are vegetables, fruits, fresh milk, cold fresh meat, etc.
Low-temperature cold storage requires the product temperature to be controlled at -18°C or -20°C. Products with many storage types are frozen meat, quick-frozen food, such as quick-frozen dumplings, quick-frozen pastries, ice cream, etc. In practical cases, the common cold storage is -18 °C.

Compared with the normal temperature warehouse, when the rack is used in the cold storage, it is usually necessary to think about the design link from the following aspects:
- Choose the appropriate rack steel material
The low temperature environment has specific requirements for the application of steel, and it should have good low temperature toughness and ductility to prevent brittle failure.
- Choose a suitable racking system
Cold storage can be described as “an inch of land and an inch of gold” without exaggeration. Selecting a suitable racking system, using every cubic meter for customers, and arriving at the warehouse application rate are the elements that the rack supply enterprises need to think about.
The combination of warehouse and rack is an ideal high-level storage system, which directly fixes the warehouse roof and side walls to the shelves, eliminating the need for warehouse construction work.
The warehouse application rate is high, and the long-term investment return rate is also high. At the same time, the technical requirements for racks are also high.

- Choose the appropriate rack surface disposal method
Spraying is a common method of surface disposal of racks. For cold storage with less stringent requirements for anti-corrosion and anti-rust, the applicability is very good, and it is economical and applicable.
Regarding spraying, the cost of hot-dip galvanizing is higher, and the cost is about 40% higher. Hot-dip galvanizing is to immerse the rust-removed steel parts in a molten zinc solution of about 500 ℃, so that the surface of the steel parts is attached with a zinc layer, so as to achieve the purpose of anti-corrosion.
If the customer has high requirements for anti-corrosion and rust prevention and is not very sensitive to cost, the surface treatment method of hot-dip galvanizing can be used.
In many cases, it can also be handled flexibly, and different surface treatment methods can be adopted according to the specific conditions to achieve the best solution. For example, the drive-in racking system, the start bay is sprayed, and the ground rails placed in the air can be hot-dip galvanized to achieve good results. Cost advantages and application effects.
- Other considerations
The design of cold storage racks also needs to consider other factors, such as the selection of welding electrodes in the cold storage, corresponding to the welding base metal material and welding process requirements, and ensuring the welding quality of the welding seam.
The characteristics of frosting in the cold storage should be considered, the weight gain should be properly considered when calculating the rack selection, and the anti-corrosion requirements of the customer’s refrigeration and defrosting processes for the structural spray coating should be considered.