To store the goods efficiently in a warehouse, various types of warehouse storage solutions are used. Among the warehouse storage solutions, pallet racking is the most popular. Today we will discuss in detail considerations for drive-in racking design.
Pallet racking is so popular as a warehouse storage solution because it is incredibly cheap. If we compare the price of pallet racks with other warehouse storage solutions, like the mezzanine floor, we will notice a massive difference in the price.
There are various types of pallet racking systems that are used in the warehouse. Some of the most common pallet racking systems that are used in the warehouse are as follows:
- Selective pallet racking.
- Drive-in pallet racking.
- Double deep pallet racking.
- Shuttle pallet racking.
Among various types of pallet racking systems, drive-in pallet racking systems are one of the most used pallet racking systems. From China to the USA, drive-in racking systems are famous in warehouses worldwide.
Drive-in Pallet Racking cost is $65-$110 for each pallet. The price range of the drive-in pallet racking system is also affordable for many warehouse owners.
In our article today, we will discuss the following things:
The following group of people will find this article especially useful:
- Warehouse owners who want to know in great detail about the drive-in racking system design.
- Warehouse owners and managers who want to know the advantages and disadvantages of drive-in racking systems.
- Warehouse managers who are looking for an expert drive-in racking system design manufacturing company.
- Academicians and researchers who want to study in-depth drive-in racking system design.
What Is Drive-In Racking?
Before knowing the drive-in racking system design, we should know the definition of drive-in racking. Now, let’s jump into the topic of this section, “What is drive-in racking?”
Drive-in racks are pre-assembled racks used for palletized storage where forklifts drive in and out of the shelves. The Drive-in racking system is made up of inner lanes that are formed by connecting sets of frames and vertical uprights.
As many SKUs are allowed by this small storage system as there are loading lanes. The quantity of pallets to be stored determines the depth and height.
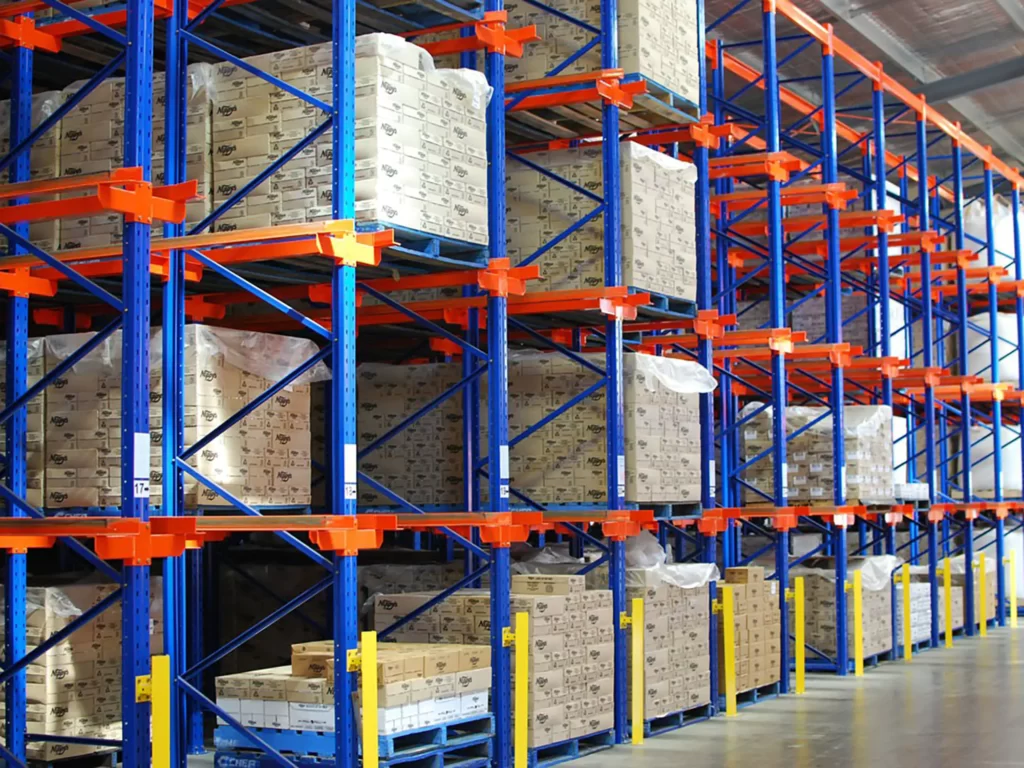
Drive-in racking is classified into two types. These are what they are:
Single Entry Drive-In Racking.
This type of drive-in racking has forklift access on only one side.
Double-Entry Drive-In Racking.
Both sides of the racks have forklift access in double-entry drive-in racking. This drive-in racking system design allows pallets to enter the rack from the back and front sides. A large beam connects the racks in the structure’s center.
Primary Components And Accessories In The Drive-In Pallet Racking System.
The following are the primary components and accessories in the drive in racking system design:
- Longitudinal upper beam
The upper longitudinal beam connects the frames in the upper area crosswise, creating gantries to secure the structure. All of the compact racking aisles must have beams installed.
- Horizontal brace
The horizontal brace is a top-mounted metal component that reinforces the compact structure.
- Frame
The frame is a fundamental component of the Drive in compact racking. These frames are made up of two uprights, diagonals, baseplates, and fixing elements.
- Frame and upright protection
The frame and upright protectors protect the installation from potential forklift damage.
- Upright
The galvanized upright is the frame’s main component. Customers can choose from upright sections and lengths to meet their drive-in racking system design requirements.
- Bracket
The metal components that support the support rails or pallet beams on each level, thus indirectly supporting the pallets, are known as brackets.
- Welded baseplate
The welded baseplate is specifically designed for frames with the highest load and height in drive in racking system design.
- Pallet beam or support rail
These horizontal profiles support the pallets on each level of the Drive-in pallet racking system. They are made of metal and are perpendicularly attached to the upright with brackets.
- Forklift guide rail
This is a floor-level steel rail that runs the length of the aisle. Its purpose is to guide the forklift as it enters the structure and protects it from potential impacts. It also helps to separate the forklift from the drive in the drive-in racking system design.
- Pallet guidance
It is located in front of the pallet racking beam or pallet support rail and assists operators when depositing unit loads. It also shields the structure from potential damage.
- Pallet backstop
Pallet backstops are preventive safety backstops whose main function is to keep the pallet from falling at the back of the aisle. This is due to an improper maneuver in the drive-in racking system design.
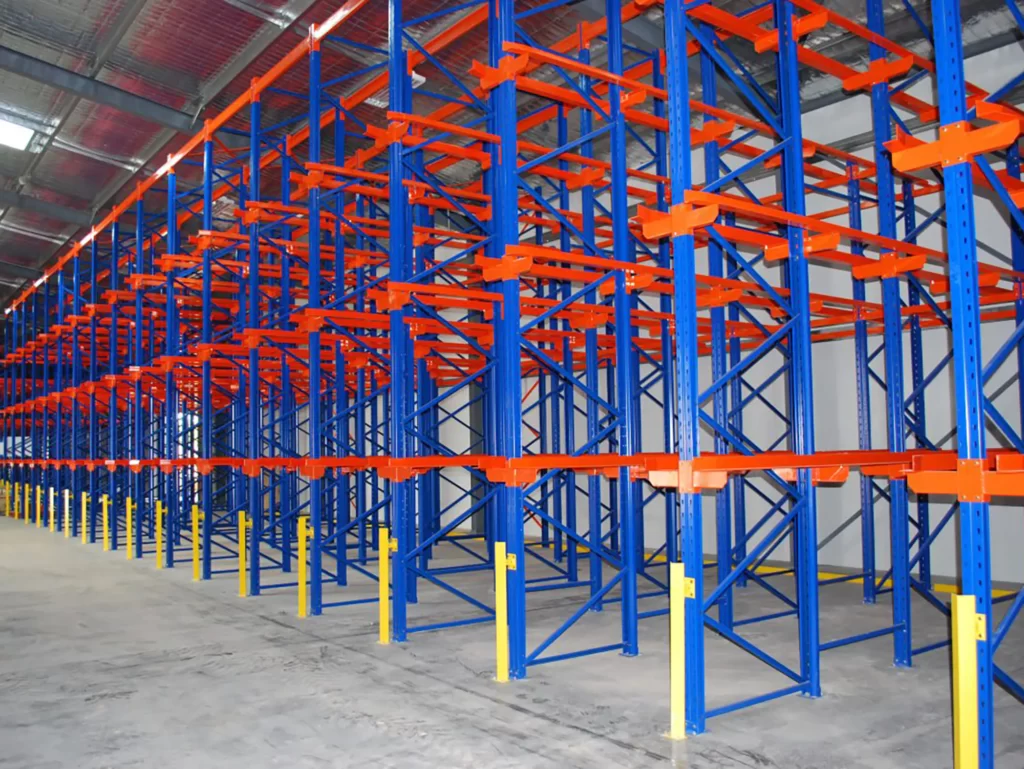
Advantages Of The Drive-In Racking System.
The drive-in racking system has the following advantages:
- This system is straightforward to relocate, modify, and upgrade as needed.
- The drive-in racking system requires minimal maintenance and assembly.
- A drive-in racking system design maximizes warehouse square footage. With fewer aisles, space is used more efficiently.
- Allows for clearly organized logistics management with complete control over inventories, traffic, and service flow.
- Load rails made of strong structural angle steel in the drive-in racking system.
- Low-profile arms that save space. Removes the service aisles found in traditional pallet racking systems.
- drive-in racking system can be specially made for your pallets and forklifts.
- Inexpensive storage strategy. drive in racking system design is one of the most cost-effective because of its low maintenance and assembly costs.
- The structure is easily assembled. drive-in racking system’s structure is interchangeable with other storage systems too.
- The structure is designed to be easily reconfigured for extension or change.
- Storage floor and height have been increased.
- In drive-in racking system, various safety accessories are included.
- Minimal stock rotation. Ideal for storing similar low-rotation loads.
Disadvantages Of Drive In Racking System.
The Drive-in racking system is not flawless. The most common disadvantages of drive-in racking system are as follows:
- The Last-In-First-Out inventory system restricts the types of products stored in a drive-in rack.
- Forklift damage to racks is more familiar with drive-in racking system. Because of the high volume of forklift traffic in and out of the system. Forklift operators will need to take a course or, at the very least, become acquainted with the new system.
- It is easier to lose items if it is not managed correctly.
- Pallets that are not in the front are difficult to reach.
The cost for Drive in racking system is reliable under various conditions. The cost primarily depends upon
- Materials,
- Freight,
- Installation,
- Amount of pallet racks installed at a time,
- Project Management Services.
You may also have to consider the maximum load of your pallets, how many lanes shall be there, and how many levels deep it shall be.
Overall, drive-in racking systems are very cost-effective and simple to assemble due to their low maintenance and assembly costs. Not only that, but its durable materials and high quality make it very practical for racking maintenance.
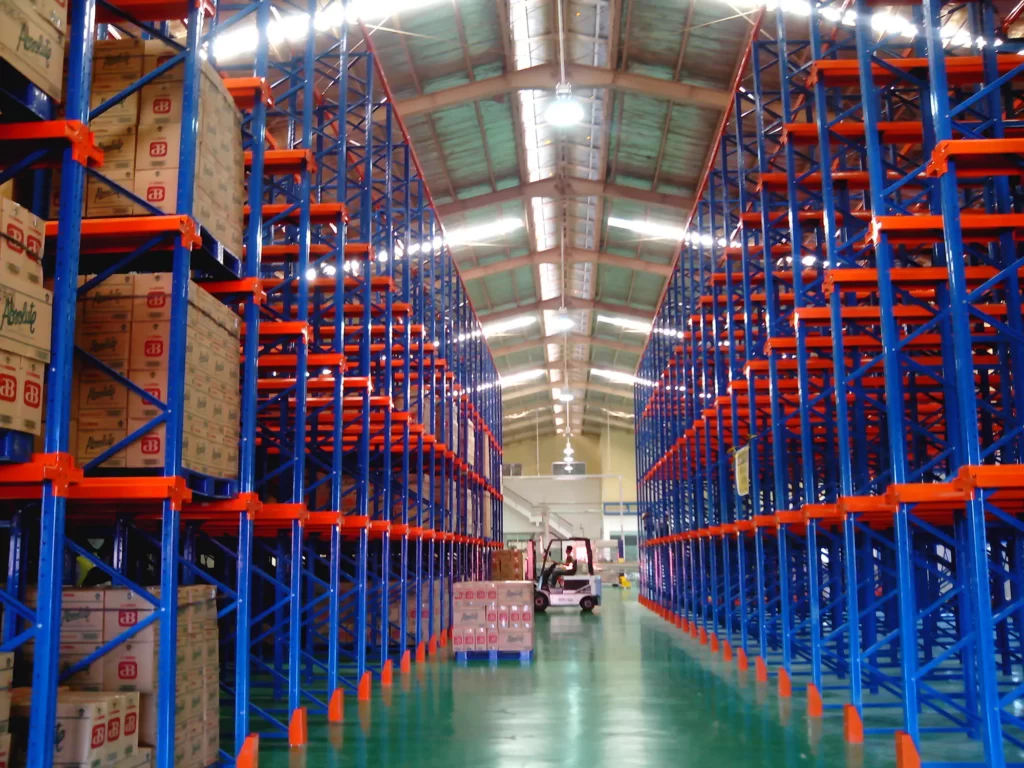
If you are looking for a reliable drive-in racking system design, consider contacting Mracking. Mracking is an expert and popular manufacturer of various types of pallet racks including drive-in racking.
Considerations For Drive-In Racking Design.
We know that drive-in racking system is highly efficient that allows for storing large quantities of similar products. It is designed to stack materials on top of each other, allowing maximum storage in a minimal amount of space.
The design of the drive-in racking system is usually built for the warehouse layout.
Drive-in racking design considerations I: height and size of the warehouse.
The warehouse size can vary depending on the type and number of stored items. The exact height and size of warehouses that use this type of racking will be based on the facility’s storage requirements.
A warehouse that holds products on pallets would often be more significant than one that holds items in cartons. drive-in racking system design is commonly utilized in warehouses with a minimum height of 10 feet and a maximum height of 15 or 20 feet.
Drive-in pallet racks are typically designed to have a width of 4 feet and a depth that can vary from 3 to 8 feet. This is assumed based on the weight of the pallet. Drive-in systems may be up to 10 to 12 pallets deep and 6 to 7 stacked pallets high.
Drive-in racking design considerations II: type of forklift.
A forklift is an essential piece of warehouse machinery. It is used for lifting and stacking heavy items. Driving directly into the rack, the forklift operator raises the pallet over the rails before lowering it to discharge the cargo.
Forklifts in drive-in pallet racking enable you to increase the number of pallet placements while decreasing the amount of floor space allocated to aisles.
The common types of forklifts are:
- Warehouse Forklift
- Counterbalance Forklift
- Side Loader
- Heavy Duty Forklift
- Pallet Jack
Warehouse Forklift
A warehouse forklift is a specialized industrial truck that moves materials, pallets, and other objects around a warehouse. Forklifts are typically powered by either electricity or a motor. They feature a lift mechanism, which helps them lift or lower loads.
Warehouse forklift entails creating a system for storing pallets on shelves accessible by a forklift. This system is intended to allow the forklift to drive into and out of the pallet racking to retrieve or deposit pallets.
Side Loaders
As the name suggests, side loaders stand sideways while their operator stands in separate compartment. Forklifts with side loaders can be utilized in drive-in racking systems. It is less efficient than reach trucks or order pickers due to the shape of the racks.
Counterbalance Forklift
A counterbalance forklift is designed to drive through aisles within drive-in pallet racking. This forklift is equipped with counterweights to help keep the lift balanced while maneuvering through the aisles.
It can navigate in small places and readily reach all pallets in the racking. So, the counterbalance forklift is also excellent for the drive in racking system. It has a low center of gravity, so it can quickly move through pallet-racking aisles.
Drive-in racking design considerations III: FIFO or LIFO storage mode.
In warehousing, FIFO and LIFO refer to how inventory moves through your warehouse. Warehouse inventory management is a critical component of logistics. It all comes down to optimization and ensuring that your items are in the right location at the right time.
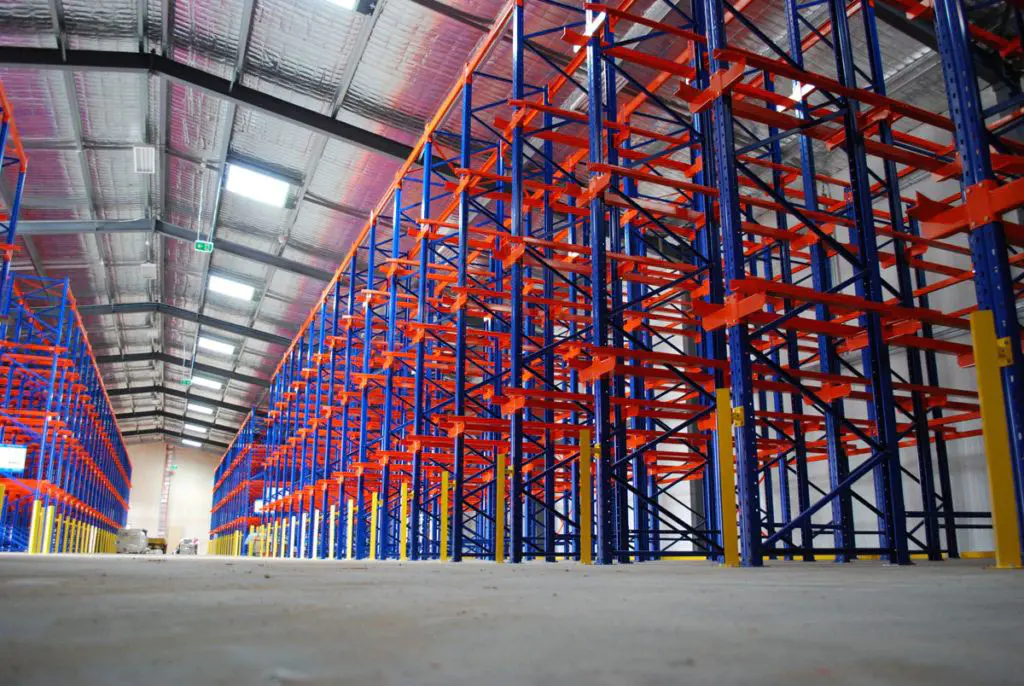
FIFO warehousing is a method of inventory management and storage that uses the “first in, first out” approach. This means that the oldest items in the warehouse are the first to be shipped out when an order is placed.
It is designed to ensure that inventory is not stored for long periods of time. This reduces the risk of spoilage or obsolescence. FIFO warehousing also helps prevent overstocking and ensure that products are fresh when shipped to customers.
FIFO represents the natural flow of inventory in most businesses. Only some businesses sell fresh things before selling older stock they have on hand. The FIFO system helps reduce inventory costs, increase efficiency, and maintain product quality.
Why Use The Fifo Method?
The FIFO method is ideal when storing products in a warehouse. FIFO boosts efficiency and improves quality control. Customers are less likely to get outmoded items since inventory is cycled often.
When to choose the FIFO method?
When you have many products and a small number of storage locations, it’s best to use FIFO. Because you can plan for the order in which products will be shipped, customers will receive their orders in the order they were placed.
FIFO is good when your product inventory is multiplying, and you need to keep track of what’s happening with each item in your warehouse. This method works best when there are multiple warehouses, and they need to be accounted for efficiently.
The opposite of FIFO is the Last In/First Out (LIFO) method. With this method, the most recent stock that comes into your warehouse is sent out first. LIFO is good for you if you are storing items that do not expire or chafe.
This inventory management method allows companies to track their inventory better than with other systems. Because they can easily see which items have been sold and which remain on hand.
LIFO also helps manage storage costs more effectively. There you can determine which items must be stored at a given location and how much space each item requires.
LIFO Rack Systems
LIFO rack systems include the following
- Push back racking system
- Double deep racking system
- Shuttle racking system
Drive-in racking design considerations IV: standard pallet size.
Before deciding on pallet size, you must consider rack types, usability, dimensions, components, and accessories. The standard size varies from warehouse to warehouse according to their needs and size.
Each deck board is 3 12″ broad and 5/16″ thick, with the standard pallet size being 48″ X 40″.
A standard pallet is 6 feet tall and can hold up to 4000 pounds. The standard pallet may weigh from 38 pounds to 48 pounds.
Application of Drive-in Racking System.
We usually need to design a drive-in racking system for our warehouses in the following situations:
- When you need an infinite amount of storage depth in warehouses with limited available space.
- When you have a high cost per square meter of floor area, it necessitates full utilization of the space.
- When using a temperature-controlled storage facility, due to the need for compaction and space optimization for proper temperature distribution and cost savings.
- Using warehouses that do not require direct access to the unit loads.
- If FILO (First In, Last Out) isn’t a problem. Like you store products in the ‘All in All out’ method.
- When it is desirable to avoid mixing SKUs within the same lane.
- When high-density storage is required (keep in mind the honeycomb effect, which confines utilization.)
- Using storage for homogeneous products and product that moves slowly. Or, Bulk supplies goods that will be stored for extended periods.
- If your product loads are fragile and cannot be stored in block stacks.
- The products in the operation channel flow to the same customer’s goods store.

The drive-in racking system requires significantly less aisle space than other types of racking. It is an excellent option for cooler applications due to the significantly fewer aisle areas. This system is frequently observed in the following industries:
- Manufacturing
- Distribution
- Beverage
- Food
- Pharmacy
- Dairy products
- Cosmetics
- Chemicals
- Electronics
- Clothing
How To Use A Drive-In Racking System?
A drive-in pallet rack system has only one entry point into the racks. A forklift driver drives into the opening and places goods pallets on the rails at the back of the racks. Workers stack newer products on top of older ones.
When pulling inventory, the driver starts with the items closest to the front, which are the most recently stocked.
Pallets are stacked on rails as high as facility forklifts can go. They could stack several pallets high. Because the forklift can only access from one side, this system allows the pallets placed last to be the first to be removed.
Because only one side requires free areas for access, this method allows products to be stored against a wall or in a corner, allowing for tighter packing of goods. Cold storage units with limited space benefit from this racking system.
However, this technique only works well with time-sensitive products or ones requiring stock rotation. On the other hand, this last-in/first-out strategy may work if products are rotated quickly.
For double-sided entry, some systems may feature entrances on both sides. The drive-in points do not link, instead having entries on both ends that connect.
Through driving, a beam supports the center and barricades. This technique enhances the amount of pallets operators can pull simultaneously by allowing two persons to access the merchandise with forklifts.
This is what you should know about the considerations for drive-in racking design. Contact Mracking for a drive-in racking system design for your warehouse.