In today’s fast-paced and competitive business environment, efficient warehouse management and storage systems are crucial for the success of any company. A well-organized and optimized warehouse not only enhances productivity but also reduces operational costs and improves customer satisfaction. As a warehouse manager or business owner, it is essential to stay up-to-date with the latest advancements in warehouse storage systems to elevate your business to new heights. In this blog post, we will explore the benefits and features of state-of-the-art warehouse storage systems and how they can revolutionize your operations.
The Importance of Optimized Warehouse Storage Systems.
Imagine a warehouse where items are scattered haphazardly, making it difficult for workers to find and retrieve products quickly. Inefficient storage practices can result in wasted time, increased errors, and decreased productivity. On the other hand, a well-designed and optimized storage system can make a significant difference in warehouse efficiency and overall business performance.
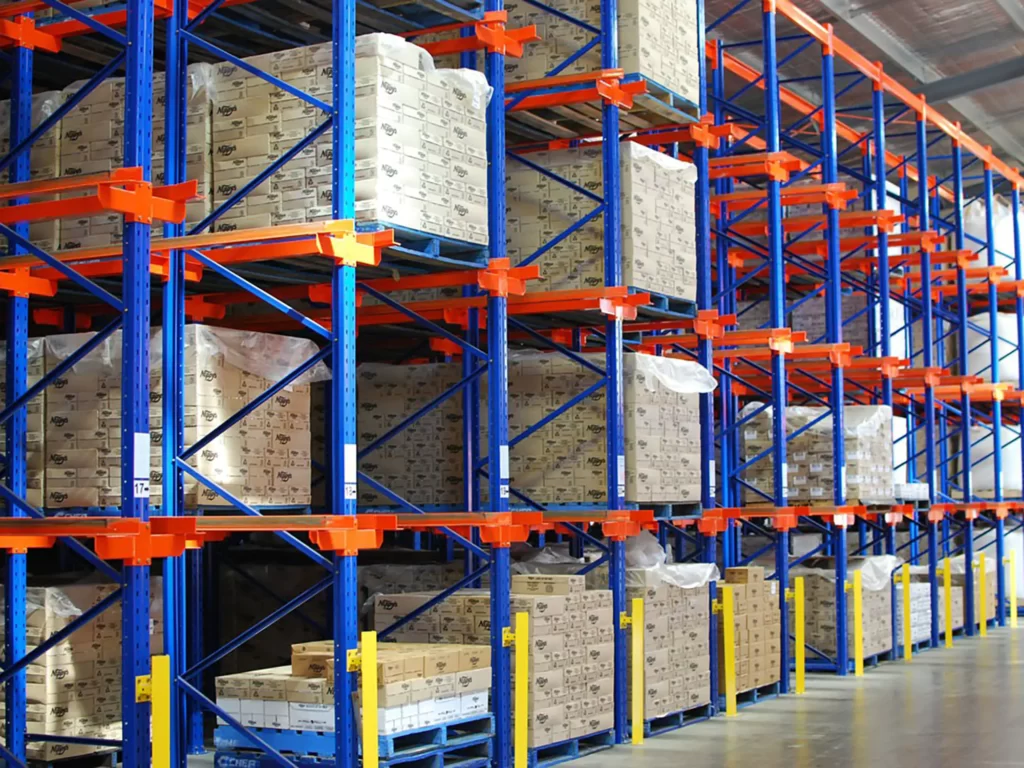
Benefits of State-of-the-Art Warehouse Storage Systems
Investing in state-of-the-art warehouse storage systems offers various benefits that can help your business thrive in today’s competitive landscape. Let’s delve into some of these advantages:
Maximize Space Utilization
One of the most significant advantages of modern warehouse storage systems is the ability to maximize space utilization. Traditional static shelving systems may not efficiently make use of vertical space or accommodate different product sizes. However, advanced storage systems, such as automated vertical storage solutions, enable you to optimize space by utilizing height, allowing multiple product categories to be stored in a smaller footprint.
Enhance Inventory Management
Accurate inventory management is critical for successful warehouse operations. Inefficient storage systems can lead to inventory inaccuracies, making it challenging to track products and reconcile stock levels. State-of-the-art warehouse storage systems often incorporate advanced inventory management features, such as barcode scanning, real-time tracking, and automated replenishment, ensuring accurate stock control and reducing errors.
Increase Operational Efficiency
Efficiency is the key to streamlined warehouse operations. Traditional storage methods often require manual intervention, resulting in slow processes and increased labor costs. However, with modern storage systems, such as automated conveyor systems and robotic picking technology, you can significantly increase operational efficiency, reduce picking errors, and minimize reliance on manual labor.
Improve Order Fulfillment Speed
In today’s fast-paced e-commerce industry, quick order fulfillment is essential for customer satisfaction and loyalty. State-of-the-art warehouse storage systems, coupled with intelligent order management software, can help expedite order picking processes, reduce order errors, and ensure timely delivery. With features like automated picking and sorting systems, your business can fulfill orders accurately and efficiently, meeting or even exceeding customer expectations.
Optimize Safety and Security
Ensuring a safe and secure working environment is crucial for any warehouse. Traditional storage systems may pose safety hazards, such as items falling from high shelves or workers straining to reach heavy loads. State-of-the-art storage systems often come equipped with safety features like automated material handling, advanced racking systems, and ergonomic design considerations. By prioritizing safety and security, you protect your workers and minimize the risk of accidents or injury.
Different Types of State-of-the-Art Warehouse Storage Systems.
Now that we have explored the benefits of modern warehouse storage systems, let’s take a closer look at some of the most commonly used systems in today’s industry:
Automated Vertical Storage Systems
Automated Vertical Storage Systems, also known as Vertical Lift Modules (VLMs), are revolutionizing warehouse management. VLMs are tall structures with vertically arranged trays or bins that store and retrieve items using an automated mechanism. These systems optimize space utilization by capitalizing on the warehouse’s height and provide quick and accurate item retrieval. By using VLMs, businesses can save floor space, reduce the risk of product damage, and significantly improve picking productivity.
Automated Conveyor Systems
Automated conveyor systems enhance warehouse efficiency by automating material handling and transportation processes. Conveyors can transport products, boxes, or pallets from one end of the warehouse to another, eliminating the need for manual labor or forklifts. These systems improve order picking speed, reduce labor costs, and minimize errors associated with manual handling. Additionally, automated conveyor systems can be integrated with other warehouse technologies, such as barcode scanners or sorting systems, to further streamline operations.
Robotic Picking Technology
Robotic Picking Technology has gained significant popularity in recent years due to its ability to increase order picking accuracy, efficiency, and speed. These robots use advanced sensors and artificial intelligence algorithms to navigate warehouses, identify products, and pick them for order fulfillment. Robotic picking technology reduces human errors, minimizes labor costs, and optimizes warehouse floor space by reducing aisle requirements. By implementing robotic picking systems, businesses can achieve faster order processing and improve overall customer satisfaction.
Warehouse Management System (WMS)
A Warehouse Management System (WMS) is a software application designed to optimize and control various warehouse operations. WMS provides real-time visibility into inventory levels, streamlines order fulfillment processes, and tracks product movements throughout the warehouse. Additionally, advanced WMS solutions offer features such as intelligent picking algorithms, integration with barcode scanning systems, and automated replenishment, making it easier for warehouse managers to manage inventory and maximize operational efficiency.
Implementing State-of-the-Art Warehouse Storage Systems.
Implementing state-of-the-art warehouse storage systems requires careful planning, thorough evaluation, and appropriate execution strategies. Here are some key steps to consider when upgrading your warehouse storage system:
Evaluate Your Current Warehouse: Start by conducting a comprehensive assessment of your current warehouse layout, storage methods, and operational processes. Identify any pain points, inefficiencies, or areas for improvement. This evaluation will help you determine the specific storage systems that will best address your needs.
Set Clear Objectives: Define your warehouse storage improvement objectives. Are you primarily targeting space optimization, reduced labor costs, or order fulfillment speed? Clearly articulating your goals will help guide your decision-making process and ensure that the implemented storage systems align with your business requirements.
Research and Select the Right Solutions: Thoroughly research different warehouse storage system providers, evaluate their offerings, and seek recommendations from industry experts. Consider factors such as system compatibility, scalability, ease of integration, and supplier support when making your selection.
Develop an Implementation Plan: After selecting the appropriate storage systems, develop a detailed implementation plan that outlines the necessary steps, timelines, and responsibilities. Consider any potential disruptions to ongoing operations and establish contingencies to minimize downtime during the transition period.
Train Your Workforce: Introducing new storage systems will require training your warehouse workers to adapt to the changes. Provide comprehensive training programs to familiarize them with the new systems, their functionalities, and safety protocols. This will ensure a smooth transition and enable your team to leverage the full potential of the state-of-the-art storage systems.
Monitor and Optimize: Once the new storage systems are in place, regularly monitor their performance and gather feedback from your warehouse team. Identify any areas that need further optimization or adjustments to maximize the benefits of the implemented solutions. Continuously seek opportunities for improvement and embrace a culture of innovation in warehouse management.
Conclusion
Investing in state-of-the-art warehouse storage systems is a game-changer for businesses looking to optimize their operations, increase efficiency, and stay competitive. By maximizing space utilization, enhancing inventory management, increasing operational efficiency, improving order fulfillment speed, and optimizing safety and security, advanced storage systems offer a wide range of benefits. Whether it’s implementing automated vertical storage systems, automated conveyor systems, robotic picking technology, or a comprehensive Warehouse Management System, upgrading your storage capabilities can elevate your business to new heights. Stay ahead of the competition, improve customer satisfaction, and streamline your operations by embracing the power of state-of-the-art warehouse storage systems.