Preparing enough warehouse storage equipment is an essential foundation for your inventory facility’s smooth and efficient operation. A well-functioning warehouse not only provides secured storage areas for your items prior to their distribution to final customers but also offers better product control to ensure on-time deliveries.
Unfortunately, many businesses nowadays still perceive building their own warehouse and furnishing it with proper gear as an unnecessary cost. Instead, they usually opt for more affordable options in the short-run, like utilizing available scattered areas in their offices. Can you imagine the heavy burden of stock management with this practice?
Thus, don’t underestimate the pivotal role of investing in warehouse storage equipment for your own facility. This article will unveil a wide variety of essential gear that you can equip for your facility. With the complete equipment list herein, setting up a warehouse will no longer be a daunting task!
Storage Equipment List For General Warehouses
Let’s keep things simple by starting with a general warehouse. What should you put in it to help it function efficiently? In this part, you will get to know the full list of essential storage equipment to prepare for your inventory facility.
#1: Warehouse Storage Cabinets
Warehouse storage cabinets, similar to those seen in many homes, are high-density steel storage boxes that not only provide instant access to inventory but also are a compact and secured method to store items.
You can store virtually everything, from bulky items to pricey machinery, in these cabinets and be assured they are always safe and sound. Warehouse storage cabinets are available in various shapes and sizes, making it simple to select a type that meets your organizational requirements. Below are some of the most popular cabinet kinds:
Plastic Cabinets
This first cabinet type is a space-saving and versatile storage solution that can hold numerous tools, supplies, and records, allowing your warehouse to be superbly organized.
Plastic storage cabinets are a preferred choice for many businesses, thanks to their various strengths like affordability, low maintenance, and resistance to corrosion and moisture.
As the name suggests, plastic is the main material for building this cabinet type. PP, PE, and PVC are the most popular choices. PE (polyethylene) is durable and waterproof, making it ideal for making outdoor cabinets. On the other hand, PP (polypropylene) is lightweight and affordable, while PVC (polyvinyl chloride) is strong and chemically resistant.
Mobile Cabinets
For busy enterprises that wish to keep their office supplies organized and accessible, mobile storage cabinets are an ideal solution. These inventory containers are especially useful for storing chemical supplies, personal uniforms, and protective gadgets.
In addition to holding stuff, mobile cabinets also provide top-notch safety for the items inside with lockable doors and drawers. Also, thanks to their add-in wheels or casters, you can easily move these cabinets from one location to another.
This flexibility provides unparalleled convenience as it enables the smooth reconfiguration of your warehouse layout, allowing better adaptation to changing demands and the efficient movement of equipment between sites.
High-Density Drawer Cabinets
When it comes to stocking and managing small tools, components, and packing materials, things can get out of control really quickly. However, high-density drawer cabinets can help you get rid of all those headaches.
These powerful drawers have full extension slides, allowing easy access to things kept inside, even those at the rear of the cabinet. Besides, when closed, these cabinets provide total protection from dust, grime, and other impurities.
The nicest thing is that you can stack these drawers or put them side by side to increase storage capacity and efficiency. Certain models come with anti-tamper and pick-proof locks, making high-density drawer cabinets an ideal storage place for sensitive items.
Heavy-Duty Cabinets
Here comes the toughest guy in the storage cabinet category. All elements in these heavy-duty containers are connected entirely by welding rather than screws or rivets, making them exceptionally resistant to tampering.
This feature makes these storage solutions perfect for industrial situations requiring high-level security, such as factories handling dangerous materials. However, consider carefully before using heavy-duty cabinets, as their all-welded construction demands high production costs, making them more expensive than other types on the market.
#2: Pallet Racking Systems
Besides cabinets, pallet racks are also one of the most important storage units in every warehouse. Oftentimes, these tools facilitate the use of your warehouse’s vertical space as to use them, you need to stack products on top of one another on numerous levels.
That arrangement offers an instant advantage: it helps optimize your warehouse space without the need to expand the facility horizontally, which requires a hefty amount of money. Atop these racks are pallets, which greatly aid in the movement of goods between different racking systems via the use of forklifts.
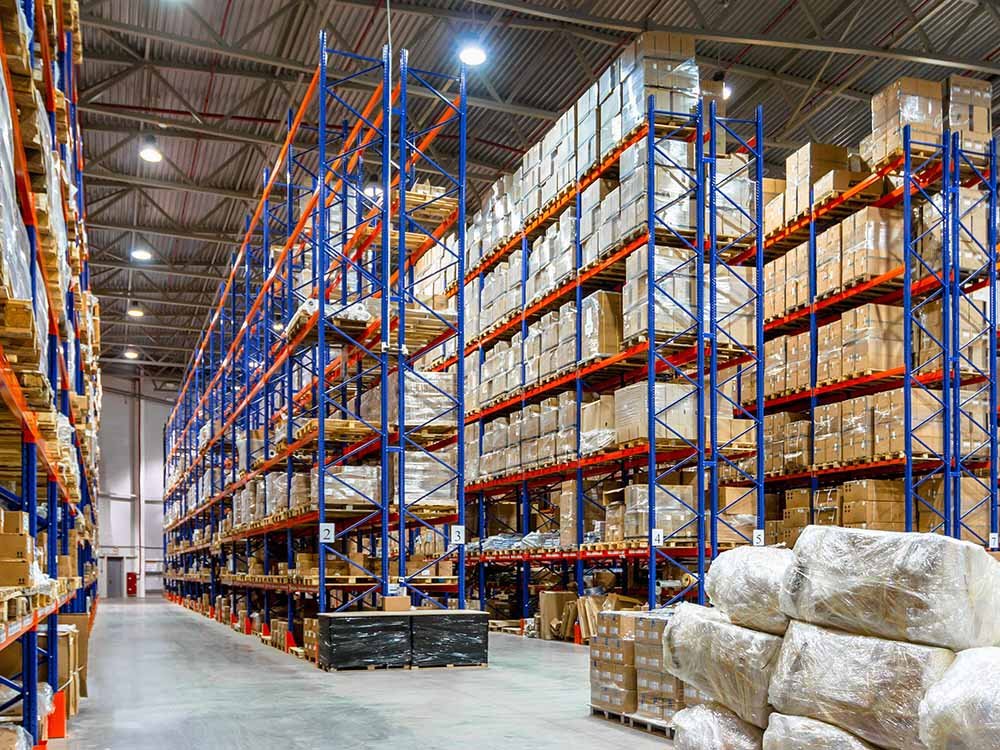
Below are several kinds of pallet racking systems that you can employ for your warehouses:
Selective Pallet Racks
This racking type is the most widely used option out there which houses products on pallets. With this setup, warehouse operators can effortlessly access the products and move them around the facility with forklifts or other lifting equipment.
A selective pallet rack comprises upright frames, horizontal beams, and other supportive elements like footplates and guard rails. Typically, this popular rack type can withstand up to 6,000 kg per level and is capable of reaching over 12 meters in height.
Push-Back Pallet Racks
Compared to the selective system, these push-back pallet racks render better storage density by facilitating up to 6 pallets deep on each side of an aisle. Intended for LIFO (last in, first out) stock management style, push-back pallet racking features a single handling spot in front.
Whenever a new pallet is added to the system, it pushes previous loads to the rear of the rack. Professionals classify this racking type into two categories based on the push-back movement:
- Push-back with rollers: With this racking system, pallets are pushed via roller beds installed on a small inclined framework.
- Push-back using shuttles: Each pallet is placed on a shuttle that travels along the racking system via a rail at a small inclination also.
Mobile Pallet Racks
When you merge the two previous rack types’ benefits together, you achieve mobile pallet racks. This racking system offers direct access to each pallet while tremendously increasing your warehouse capacity, which is a game-changer for high-density inventory.
This system consists of mobile bases or chassis attached to fixed tracks on the warehouse floor. The base, on which pallet racks are placed, is outfitted with a remote push-pull system and an electrical motor, enabling the racks to move while only opening for one lane for forklift access.
#3: Multi-Tier Shelving Solutions
Often implemented in warehouses with limited floor areas but have the potential for height expansion, this multi-tier shelving system is a brilliant storage solution that maximizes vertical space and is capable of doubling your facility’s inventory space.
In essence, this solution involves the arrangement of cabinets or shelves across multiple levels. By tapping on those unused but available vertical areas, the multi-tier shelving solution facilitates the storage of a greater quantity of goods and ultimately enhances the overall storage capacity.
But when going too high, some may question how they can access those items lying on top. Well, the answer is simple. Access to each tier is possible via various means, such as main aisles, cross aisles, and staircases.
Another frequently asked question is how high you can go with multi-tiered storage. Theoretically, this inventory solution can utilize all your warehouse height, but the maximum cap is usually 12 meters.
#5: Mezzanine Flooring
Technically speaking, mezzanines are more of an upgrade than equipment, as their integration into your warehouse requires high degrees of customization. In essence, you are simply elevating the existing aisles to create a second floor, which will provide additional storage space and work areas for employees.
Instead of limiting your warehouse to just a single level, mezzanines have the potential to offer up to two or even three floors. Thanks to recent technological advances, designing and installing mezzanines is easier than ever before while still complementing most of your existing warehouse layout and optimizing inventory space.
#6: Wire Partitions
Storage demands vary significantly from one facility to another. While some focus on maximizing the storage capacity, others demand top-notch security for the items stored within, maybe because these items are sensitive or of extremely high value. In such cases, wire partitions are the most vital solution to enhance warehouse safety.
By using wire partitions, you can effortlessly control access to areas designated for the storage of your important items, such as medicines or chemicals. Practical additions like wire partitions also effectively prevent damage or contamination to your goods and allow you to divide spaces without having to undertake extensive renovations.
#7: Lifting Apparatus
Suppose that you have fully loaded your warehouse with racks. Now you need to place pallets on those storage systems. Well, most standard pallets (including goods) weigh up to 2 tons, so manual picking is impossible. In such cases, lifting equipment like forklifts is a must-have solution.
Lifting devices serve not only to elevate loaded pallets onto racks, but also to facilitate their movement throughout the warehouse. However, when selecting the appropriate lifting equipment, it is essential to consider various aspects, including the shelf’s height.
Improper or low-quality lifting gear can wobble during operation, which may damage your products, cause accidents to the working staff below, and eventually halt your warehouse operations.
Despite the relatively high expenses, these devices offer useful benefits that can justify that upfront cost. Such benefits include a reduction in manual labor, simple configuration, and applicability in various contexts. Besides the typical forklifts, there are some other lifting equipment that you can consider, such as hand trucks, pallet jacks, cranes, and castors.
#8: Conveyors
Warehousing doesn’t revolve around just storing goods. It also entails the transportation of inventories within the facility. To do that efficiently and precisely, besides handpicking, you can utilize certain material handling machines, one of which is the conveyor.
As opposed to performing material movement manually, conveyors can automate the process, thus accelerating the goods flow and resulting in time and labor savings. Furthermore, by minimizing human intervention, they can greatly reduce the risk of injuries, which can occur during the use of forklifts.
Another benefit of this automated gear is that fewer errors occur while the times for processes like picking, weighing, sorting, and packing are significantly improved. However, please note that conveyors require a higher initial investment. So, make sure to plan your budget before considering this piece of equipment.
But if you are financially available, you can consider some of the most popular conveyor types below:
- Belt conveyor: This system comprises a closed loop of carrying belt that rotates around a minimum of two drums (or pulleys).
- Chain conveyor: This conveyor type typically consists of an uninterrupted chain that traverses a predetermined path under the guidance of tracks or rollers.
- Gravity roller conveyor: Unlike the two above kinds that rely on power to move the goods, gravity roller conveyors utilize gravitational forces to shift items along a series of rollers.
- Specialty conveyor: This particular system is designed to meet specialized warehouse demands with its tailored solution. Some examples include vertical conveyors (which facilitate vertical transportation), overhead conveyors, and accumulating conveyors.
#9: Dock Equipment
Dock apparatuses are of the utmost importance to ensure the safety of the high-traffic docking area, which serves as the intersection of shipping and receiving products. These devices facilitate the movement of items from and to the vehicles and thereby optimize your warehouse workflow.
Selecting appropriate dock equipment can improve warehouse efficiency, customizability, and safety, given the growing concern for providing enough protection for your employees.
If you are still unsure what dock equipment actually is, let’s explore a few representatives below:
- Dockboards: These gadgets facilitate the movement of personnel, forklifts, and carts between the dock and the trailer. They are predominantly made of steel or aluminum.
- Truck restraints: Also referred to as vehicle restraints, these devices help impede the departure of a transport vehicle while it is being loaded or unloaded.
- Wheel chocks and wedges: Despite their importance in keeping warehouses safe, these gadgets are often neglected. Wheel chocks and wedges are mandated at all loading docks where vehicles load and discharge goods.
- Yard ramps: These serve as a means to elevate materials into a vehicle container or to descend them to ground level.
#10: Packing Equipment
Warehouses cannot function properly and efficiently without essential equipment for packing, which means encasing products or devising a receptacle to offer extra protection and easy handling.
High-quality packing equipment is capable of increasing your staff productivity by facilitating a quicker packaging process. It also decreases labor expenses and ensures product consistency.
Additionally, packaging devices streamline stock control by eradicating the need for product separation, thereby saving a lot of time. Certain popular packing equipment includes stretch wraps, industrial scales, and packing tables.
Cold Storage Equipment List For Special Demands
Now that you know a pretty complete list of storage equipment for general warehouses, let’s dig a bit deeper into the cold storage equipment list. These specialized facilities require numerous working conditions, which can only be achieved through the use of special apparatuses. Let’s find out what they are below.
#1: Coolants
Regarded as the heart of cold storage warehouses, coolants or refrigerants are fluids that help transfer heat from one area to another, thereby providing a cold atmosphere for the first place.
Among the various coolant options out there, anhydrous ammonia and Freon gas are the most popular selections. While ammonia is affordable, it can be hazardous and flammable. On the other hand, Freon gas is incombustible and pretty harmless, but it has a higher price tag.
#2: Refrigeration System
This umbrella term refers to a series of core components like condensers, compressors, expansion valves, and evaporators that put coolants into use.
By continuously compressing and vaporizing refrigerants, the refrigeration system helps maintain temperatures within the intended range by absorbing heat inside and delivering it outside.
#3: Insulation Panels
If coolants bring about the low temperature, insulation panels help maintain that cold environment in the inventory facility. This critical equipment can be made of a plethora of materials, ranging from fiberglass and mineral wool to cellulose and polyurethane.
Each material possesses a specific insulating power, indicated by its R value. This figure, ranging from 1.5 to 7, measures how well the material can withstand heat. Among the options above, fiberglass has the lowest R value, while polyurethane has the highest figure.
#4: Cold Storage Doors
Unlike doors in traditional warehouses, cold storage doors must be completely airtight, watertight, and possess superior thermal insulation to prevent temperature loss. These gateways often come with functionalities like heated gaskets to avert the accumulation of ice and guarantee a consistent hermetic seal.
Depending on how the doors move, there are some options you can consider, such as sliding, swing, high-speed roll-up, vertical-lift cold doors, and air curtains. For cold warehouses that demand extremely strict climate regulation, controlled-atmosphere doors are the go-to solutions.
#5: Cold Storage Racking Systems
Another indispensable item in cold storage warehouses is the racking system dedicated to this chilling chamber. Unlike conventional racks, cold storage racks must be made of more durable materials, such as stainless steel, to ensure they can overcome the harsh climate inside the cold room.
Other than that, cold storage shelving systems are similar to normal types in terms of categorization. You still have those familiar kinds like selective, drive-in, push-back, and mobile racks. AS/RS and pallet shuttle solutions are also popular shelving systems for cold warehouses.
#6: Monitoring System
Modern monitoring and alert systems are also critical, as they continuously observe and record many vital parameters in cold storage warehouses, including temperature and humidity. These inputs are like real-time updates on the situation inside, which are very important for the smooth running of these facilities.
Whenever parameters deviate from the predetermined range, immediate alerts are generated, enabling prompt corrective measures to be implemented. Without these timely notifications, perishable items inside the cold warehouses can be spoiled in minutes.
#7: Power Backup Equipment
Cold storage warehouses demand a constant supply of electricity to maintain their proper functionality: keeping items fresh in low-heat environments. But what if power outages happen and interrupt these facilities’ operations? Well, let’s get rid of those concerns with power backup equipment.
Backup generators are often fueled with natural gas or diesel. Having them in your cold storage warehouse is a true peace of mind, as they guarantee smooth and uninterrupted operations, thereby ensuring all items stored inside are always safe and sound.
#8: Adaptive Lighting And Fans
In order to optimize visibility and reduce heat production, LED illumination solutions are often incorporated into cold storage warehouses. These adaptive lighting systems are specifically designed to function reliably at really low temperatures and flawlessly illuminate aisle areas with narrow light patterns.
Besides a reliable lighting system, efficient air circulation via fans is also essential to ensuring consistent temperatures. By ensuring that cold air is distributed uniformly, fans can eliminate heat stratification and promote stable product conditions.
Conclusion
In short, opting for the appropriate warehouse storage equipment will result in enhanced levels of productivity and safety, thereby leading to smoother operations and, ultimately, better customer satisfaction.
This article has provided a full list of essential must-have items for your inventory facility, including both general warehouses and specialized cold storage premises. While some of the recommendations require big upfront expenses, they will definitely pay off in the long run through efficient operations.
And of course, depending on your specific situations, you can flexibly choose to keep certain items on this list while dropping others. Therefore, think carefully about your inventory demands before making the equipment list.