Generally, a warehouse is a place where one stores goods for eventual distribution. Warehouses typically have large spaces, heavy machines and equipment, railings and even industrial structures (like Mezzanines) built inside them.
More so, some warehouse spaces are used for retail or office spaces. In a typical warehouse, there is a high amount of human labor. To mention a few of what people do in a warehouse, some are supervisors and managers to ensure the smooth running of the day-to-day activities, some are transporters, some operate the machines in the warehouse, and while some keep stocks.
This points out that there is also a high number of humans in a warehouse. This simple fact necessitates the need for safety measures in a warehouse lest accidents happen and there is a high mortality rate within the facility.
Also, because there are heavy machines and huge industrial structures inside the warehouse, there is also a need to put safety measures in place to mitigate any potential accident that might occur. This safety measure is known as a warehouse safety checklist.
This article will espouse some warehouse safety checklist, but before getting to that, it is important to first understand what the concept entails.
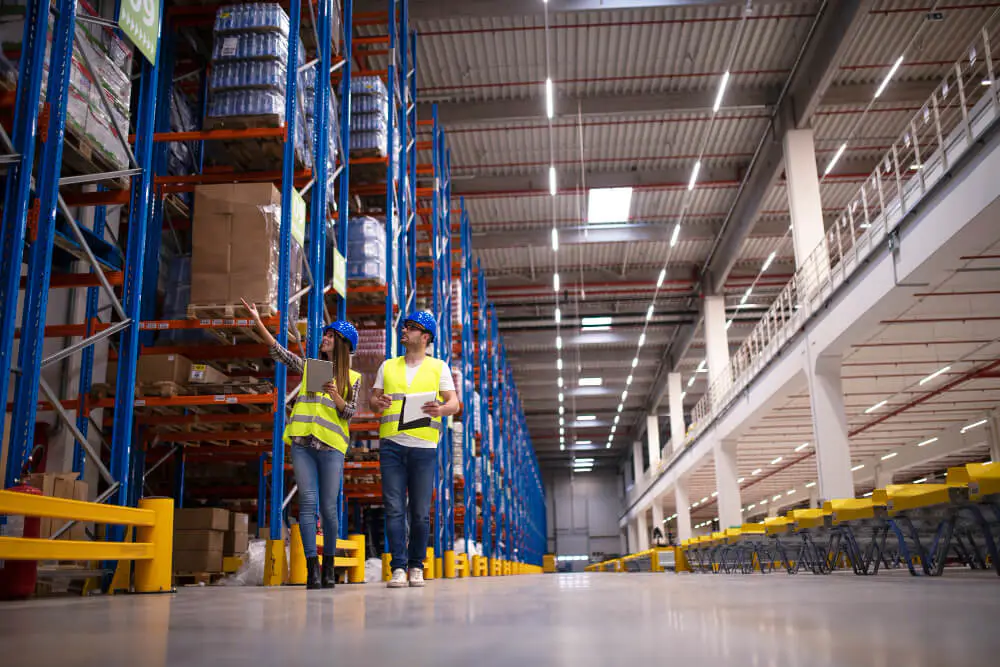
What is a Warehouse Safety Checklist?
Basically, a warehouse safety checklist is a list of safety measures that warehouse workers must adhere to. There are warehouse workers who are in charge of safety procedures and measures. These workers are called the “warehouse safety workers.” They are the ones responsible for implementing the warehouse safety checklist.
The warehouse safety workers use the warehouse safety checklist as an inspection tool to check, measure, and assess the extent of safety compliance, mitigation of risks and hazards and generally ensure the safety of the warehouse work environment.
A warehouse safety checklist will help the warehouse safety worker to pinpoint where potential hazards are around the warehouse, help determine where there should be labels and safety signs around the building, where there are no danger and safety signs but there otherwise should be, and where danger is at its highest. With the warehouse safety checklist, the warehouse safety worker can also determine the most appropriate safety measure in particular areas and all around the warehouse.
The end goal of a warehouse safety checklist is to identify risks and potential danger, mitigate them, and avoid any potential accidents as much as possible.
Why is Having a Warehouse Safety Checklist Important?
Warehouses accommodate heavy machines, chemical substances, numerous electrical cables, heavy industrial structures, and a large number of goods. This makes the warehouse a dangerous place if there are no safety measures in place to protect workers from hazards.
This is why one must know the warehouse type, the kind of goods in the warehouse, and its structures. Knowledge of these will allow one to assess the risks and know the potential dangers around the warehouse, and the areas where these dangers may occur. Failure to know this will leave the workers exposed and may lead to accidents which may cause severe injuries or even a high rate of workers’ mortality.
Accidents that may occur in a warehouse include:
- forklift accident, which can severely injure workers or even lead to death
- Falls
- Exposure to dangerous chemical substances
- Injury sustained due to failure to wear personal protective equipment
- Electrocution
- Injury from heavy machines in the warehouse
- Fire burns
However, with a warehouse safety checklist, one can mitigate these potential risks and dangers. A warehouse checklist primarily ensures two things: financial security and protection of the lives of workers.
Financial Security: With a warehouse safety checklist, you can rest assured of little to no accidents occurring in the warehouse. It will result in the firm not having to spend high medical bills due to warehouse accidents.
Protection of Workers’ Lives: With a safety checklist, there are standard safety procedures and measures put in place to protect workers always. Also, the checklist will seek to assess risks and then provide for measures to avoid these potential risks.
What Are the Items on a Typical Warehouse Safety Checklist?
Typically, a warehouse safety checklist contains every item that ensures the assessments of every potential risk, danger, and hazards in a warehouse facility. Also, you may tailor the checklists to the type of warehouse. For example, a chemical warehouse may have the need for biological and chemical hazard labels and warning signs, while an industrial warehouse may not need such warning signs.
Further, a warehouse safety checklist checks and assesses all areas, equipment, and structures in the warehouse. It also seeks to check for the appropriate protective and safety measures that can be utilized in the warehouse.
Below is a list of items that you can see in a typical warehouse safety checklist:
- Fire safety
- Hazard warning signs
- Highly flammable equipment
- Danger areas
- Chemical/biological safety
- Protective measures and equipment
- Ladder safety
- Electrical fittings safety
- Compressed gas
- Availability of first aid kits
- Highly combustible equipment
- Loading dock safety
- Emergency exit doors
- Emergency procedures
- Work surface safety
- Cleaning and maintenance
- Employee safety practices
How Do You Do a Warehouse Safety Inspection Using the Warehouse Checklist?
A warehouse safety checklist helps you to put things into perspective and prioritize crucial safety measures. In the US, the OSHA conducts safety inspections in every warehouse, however, you do not need to wait for any agency’s safety inspection before carrying out your safety inspection using the safety checklist.
What should you do to carry out a safety inspection?
Supervision: Take a walk around the entire area of the warehouse. As you walk around the area of the warehouse, hold a note and take down every single detail of the entire area. Note the things that are out of place and anything that could potentially be dangerous to the workers. Also, when walking around, you should have your safety checklist with you. You can then tick the safety checklist as you walk around the area. That way, you can know if every part of the warehouse is up to the desired standard safety measure and you will know the areas that are lacking, and how to resolve the observed challenges.
Have Standard Safety Measures: As mentioned earlier, some countries have a set of safety guidelines and measures that are expected of every warehouse to put in place to ensure safety of all their workers. After preparing your safety checklist, you need to compare it with what is required by the monitoring agency. You need to know if the practices in the warehouse are standard, and if the safety protocols meet the required standard set by the authorities. You can visit the monitoring agency’s web page to see if they have a warehouse safety recommendation for different warehouse types. You may compare your safety checklist with what the authorities recommend.
Jump into Action: This is particularly essential when you notice anything out of place in the warehouse or any area that may require the implementation of safety measures. Whenever you see the need for safety measures, you need to immediately take down what kind of safety measure is required in that area, and then, jump into action. This is so that the next time you conduct safety inspection, the required safety measure is already put in place in that area.
A typical Warehouse Safety Checklist Document
- Easy to read and understand: A typical warehouse safety checklist should be easy to read and understand. You should not need a safety professional before you can conduct a safety inspection using the checklist. It should be well defined and easy to input the necessary details in the necessary spaces.
- Sections: There has to be different sections in a warehouse safety checklist. Each section may be split into areas of the warehouse or the different types of safety measures. For example, a section may be about fire safety measures, another may be hazard communication, another may be about emergency exit routes and procedures. Each section should address the safety measure that should be required in every area of the warehouse. A section may include the general safety check and then another section may be about specific safety checks and measures in specific areas of the warehouse.
- Causal items: A well prepared warehouse safety checklist is not just all about what isn’t working well. If your checklist only takes the faults and damages into account, then it is not comprehensive enough. A comprehensive checklist also takes cleanliness, and may other causal factors for injury and accidents into account.
- Remarks and grades: You need to provide for a section where you can put a remark or grade for each of the section of the checklist. That way, you can note if the safety measures and procedures in place are good, bad or needs upgrading. You can talk about the status progress of a safety measure you are putting a place and also give a general remark about the overall safety of the entire area of the warehouse. A section for remarks ensures that you know exactly how functional every types of safety measures in the warehouse is.
Sections of a Warehouse Safety Checklist
As mentioned earlier, a warehouse safety checklist must be in sections and each section should cover the specific types of safety in specific and the general area of the warehouse. Below are the safety measures list that may be found in a standard warehouse safety checklist.
- Damages
A warehouse safety checklist should have a section that prompts you to check for every kind of damage within the warehouse. You may check damages on the ceiling, roof, inner and outer structure, mezzanines, pipes, electrical conduits, floors, doors, walls, among others. Whenever you are conducting a safety measure and you notice any damage in any part of the warehouse, note the type of damage and its location. And then remark how bad the damage is in the remarks section of the safety checklist.
- Obstructions
An obstruction is basically when an item in a warehouse hinders the effectiveness of a safety measure. For example, when there is a stack of goods packed around the emergency fire exit door, the goods are obstructing the emergency fire exit door from becoming accessible in case of a fire outbreak in the warehouse. It means that either workers have to create another exit route or they have to start to move the goods, equipment, or items blocking the exit door. An ideal and comprehensive warehouse safety checklist should check for obstructions.
- Cleanliness
Cleanliness is also a safety measure. When the warehouse environment is hygienic, it becomes a safe and excellent working condition for workers. Although maintaining perfect hygiene may be unattainable in a warehouse, it is crucial to do a thorough and consistent cleaning of the environment. You should check if the trash has been properly disposed, if the area is kempt, and if there are any used items that may be dangerous to workers’ health lying fallow.
- Fire hazard safety
Fire hazard safety check is important. You need to check if there are fire extinguishers around the area and if these extinguishers work. Other fire safety equipment include a fire hydrant (if necessary), a sprinkler, fire alarms, fire warning signage, and fire safety protocols.
- Loading docks
Most warehouses have a loading dock or bay. Thus, it is absolutely important for a warehouse safety checklist to have a section for checking the loading docks. Check for the equipment in the dock, the forklifts, the rails, and check for obstructions on the dock.
- Stairs
The stairs are another important part of a warehouse. It is how workers move from one point to another in a warehouse. Also, stairs are typical in warehouses with mezzanine structures. Thus, prioritize checking the stairs for safety. Check for the railing, probability of a fall, the integrity of the design, and the height.
- Use of PPE
Since there are a lot of heavy machinery and dangerous items in the warehouse, it is important for workers to wear specific PPE required for certain tasks. Common PPE include hard hats, helmet, gloves, jackets, overalls, safety shoes, and many more. From the checklist, you should see if there is enough PPE in the warehouse, if there is provision of specific PPE for a specific task, and if the workers are correctly using PPE when they are carrying out tasks.
- Signs and labels
Signs and labels are a means of communication to workers and non-workers alike on safety measures and the potential dangers in an area. For example, if an area of the warehouse has a faulty or exposed electrical cable, there should be a sign of high alert of the exposed cable in that area of the warehouse.
That is why signs and labels are included in a standard warehouse safety checklist. Signs and labels are not just for hazard communication. They also ensure the orderliness of everything in the warehouse. They prevent workers from using the wrong items while at work. Further, a proper label of items and equipment ensures a smooth and fast running of the warehouse.
- Hazard communication
Some warehouses, especially ones where hazardous items (like chemical substances) are stored have a higher risk factor. Thus, it is essential to correctly label every dangerous item and have signage all around the warehouse area that informs workers and visitors on where to go around the area and what not to tamper with. It is where hazard communication comes in. At the remarks section of the warehouse safety checklist, you need to weigh the effectiveness of the communication of hazardous areas and items.
- Ventilation
To achieve an excellent working condition, there must be a proper ventilation of the warehouse, lest workers choke when working. Thus, a standard warehouse safety checklist provides for checking of the ventilation around the warehouse and if there are any obstructions to ventilation.
- Electrical fittings
A comprehensive and standard warehouse safety checklist checks for the electrical fittings around the warehouse. Check for the cables and wires to see if there are loose wires or exposed cables that may be hazardous to workers. Check if there is an electrical problem in any area of the warehouse and the overall state of the electrical fittings in the warehouse. It will mitigate the risk of electrocution or fire outbreaks due to electrical faults.
However, before you can have a warehouse safety checklist, you first need to have safety rules and measures in place.
Warehouse Safety Rules and Measures
To put safety measures and rules in place, there is the need for consideration of the warehouse size, space, policy, structure, equipment, procedures, and the goods in it. All of these will serve as influencing factors on the kind of rules and safety measures that are set in place which will ultimately play a key role in the warehouse safety checklist.
Setting a warehouse safety rules is not really challenging, as long as you put the factors mentioned above into consideration and ensure the rules are in consonance with the safety implementation agency in your country. For instance, the body that regulates warehouse safety rules and measures in America is the Occupational Safety and Administration health Agency (OSHA).
To create a warehouse safety checklist, there are some safety rules to put in place. Below is a list of safety rules that are in line with the OSHA regulations
- Use of Safety Equipment
There are safety equipment that can be used in a warehouse to prevent accidents or reduce the magnitude of disaster that may occur in the case of an accident in the warehouse. Use of gloves, wearing of helmets, or wearing of personal protective equipment (PPE) in an industrial warehouse can prevent high mortality in case of accident, lessen the severity of accidents, and generally protect an individual from harm or injury.
It is essential to have these types of equipment in your warehouse and then ensure that all workers use them protectively. It will ensure a safe working environment and even prevent you from having to expend funds on hospital bills in case of accidents.
- Evaluate Safety Hazards
It is important that you conduct a risk assessment of safety hazards in your warehouse to prevent workers from falling into harm that could be easily avoidable. After proper evaluation, you can then eliminate these hazards by displaying signs around the warehouse of potential hazards around the area. These signs can also instruct workers on what to do in the areas of potential hazards
- Prevent Electrical Accidents
Warehouses have electrical fittings all around the area which can pose a danger. There are electrical wires around some areas and also, some areas could be the main power grid of the warehouse. These areas can be more dangerous than other sections of the warehouse. It is crucial to control these electrical hazards by ensuring that you cover any wirings around the warehouse. Also, if there are any electrical faults, it is advisable to attend to it immediately.
- Use Labels and Signs
Ensure to use labels and signs in all areas of the warehouse to guide both workers and visitors in the warehouse of any potential danger or anything that might result in an accident. For example, in a warehouse that houses dangerous chemicals and heavy dangerous machines, there should be signs which tell what part of the building is where the chemicals are stored and how dangerous the segment is. There are different types of labels and signs you can use in a warehouse. They include the following:
- Caution sign
- Danger sign
- Warning sign
- Chemical hazard sign
- Safety sign. E.g. need to wear Personal Protective Equipment (PPE)
- Implementation of a Safety Protocol
Safety protocols are especially crucial in a warehouse. Warehouse workers should know what to do when there is a danger alarm around the warehouse. For example, in the case of fire, there should be a fire exit door where all workers in the warehouse can take their exit from the warehouse without sustaining any injury.